Tunnel Dryers

Tunnel Dryers
Kerone Engineering Solutions Ltd. manufactures numerous types of tunnels in a range of dimensions, with variations in the tunnel’s construction, tray capacity, length, conveyer speed (adjustable), air circulation rate, control panel, and other factors. Tray dryers are improved by tunnel dryers because they enable the trays to move around. The material that needs to dry is fed in at one end and recovered at the other end of the air-heated tunnel. Due to its construction’s tunnel-like appearance, the term was formed. The drying process can be finished in a tunnel drier while the material is being transported down the tunnel, depending on the technology chosen.

Efficiency and Performance
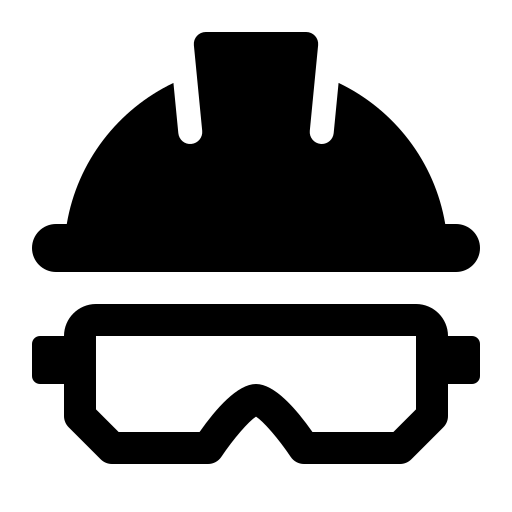
Safety Features
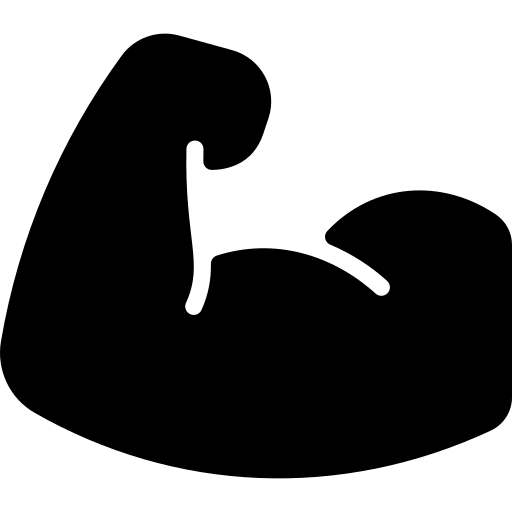
Durability and Build Quality

Customization and Versatility
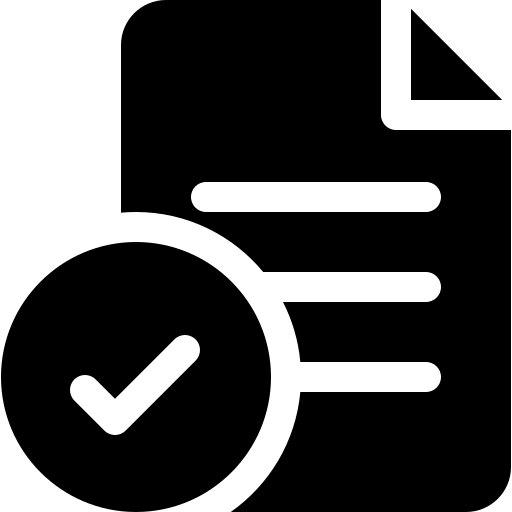
Compliance and Certifications
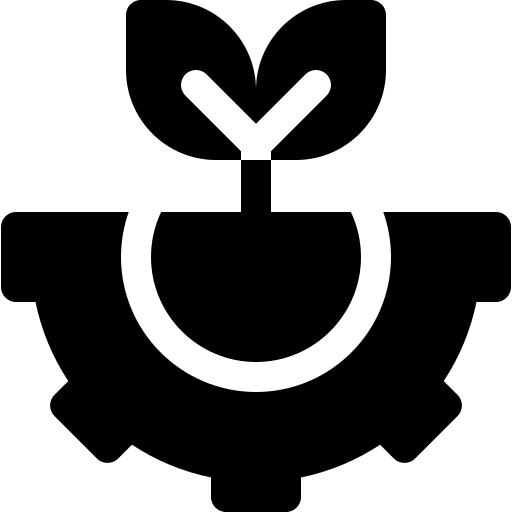
Environmental Considerations
- Microwave Heating Dryer
- Radio Frequency Heating Dryer
- Conventional Heating Dryer
- Infrared Dryers
- Hot Air Dryer
- Pneumatic/ Flash Dryer
- Spray Dryer
- Drum Dryers
- Box Dryers
- Heat Pump Dryers
- Imperial and Band Dryer
- Coal/Briquette Dryer
- Tunnel Dryers
- Contact Drying- Steam Cylinders/Cans
- Fluidised Bed Dryers
- Rotary Dryers
- Tower Dryers
- Tray Dryers
- Fish Dryer
- Spiral Conveyor Dryers
- Microwave Spices Dryer
- Food Dryers/Food Dehydrator
- Freeze Dryers
- Coir Pith Dryers
- Conveyorised Organic Waste Dryers
- Screw Dryer
- Rotary Dryer
- Fluidised Bed Dryers
- Spray Dryers
- Sludge Dryers
- Agitated Thin Film Dryers
- Rotary Tube Bundle Dryers
- Biomass Dryer
- Manure Organic Fertilizer Dryer
- Cocopeat Coir Dryer Machine
- Coal Dryer Machine System
- Carbonization Machine
Kerone Engineering Solutions Ltd. manufactures numerous types of tunnels in a range of dimensions, with variations in the tunnel’s construction, tray capacity, length, conveyer speed (adjustable), air circulation rate, control panel, and other factors. Tray dryers are improved by tunnel dryers because they enable the trays to move around. The material that needs to dry is fed in at one end and recovered at the other end of the air-heated tunnel. Due to its construction’s tunnel-like appearance, the term was formed. The drying process can be finished in a tunnel drier while the material is being transported down the tunnel, depending on the technology chosen.
A tunnel dryer is a specialized drying equipment widely used in various industries for the efficient and uniform drying of products. This innovative machine consists of a long tunnel-like chamber through which the products pass on a conveyor belt, undergoing a controlled drying process. The content of a tunnel dryer encompasses several key components and features that contribute to its effectiveness and versatility.
To ensure uniform airflow and heat distribution throughout the tunnel, tunnel dryers are equipped with a series of fans or blowers. These fans facilitate the movement of heated air, effectively circulating it around the products. By maintaining consistent airflow, the tunnel dryer achieves even drying across all parts of the product, minimizing moisture variations and reducing drying time.
To control the drying process, tunnel dryers feature a comprehensive control system. This system allows operators to set and adjust various parameters such as temperature, airflow rate, and conveyor speed. By fine-tuning these variables, the drying conditions can be optimized to suit the specific characteristics and moisture content of the products being dried. Additionally, modern tunnel dryers may employ advanced sensors and automation technologies to monitor and regulate the drying process more accurately and efficiently.
The conveyor belt is another essential component of a tunnel dryer. It transports the products through the drying chamber at a controlled speed, ensuring a consistent exposure time to the heated air. The belt is typically made of a durable and heat-resistant material, capable of withstanding the drying temperatures and the weight of the products being processed.
Features
- Insulated inner surface for optimal energy efficiency and to prevent energy loss.
- A high-quality heat exchanger demonstrates that the air is wet.
- Improved operating life and handling.
- Conveyors with rollers or belts to move the material.
- Solidly built to withstand moisture-containing materials and shifting situations.
- A system that circulates air to increase airflow and shorten drying times.
- Various length and width ratios are available.
- A control system that is precisely constructed and calibrated.
- Integrated into a fully or partially automated structure.
- Minimal losses to the environment.
- Temperature and conveyer speed settings on a touchscreen control panel.
- The technology of your choosing can be supported.
- Consistent drying of all input materials.
- Durable powder coating.
- It is possible to set up numerous drying zones.
Application
- Fruits and vegetables are dried.
- Ink and paper drying.
- Coat drying in the coating line.
- Packing materials drying.
- Plastic spoons, injectable vials, caps, and other items are dried.
- Pharmaceutical pills and powders are dried.
- Containers and packing materials should be sterilized.
- Textile fabric drying.
- Fresh fruits, vegetables, eggs, and roots are dried.
- Food processing and confections drying.
- Ceramics in molds are drying.
We at Kerone Engineering are pleased to be your first choice for all engineering solution needs. With great pleasure, we announce that we can now provide our excellent complete engineering solutions not just state-wide but now throughout India.
We expand to ensure that our innovative and dependable heating, cooling and drying products are available to various industries across the globe because of our dedication to quality and client satisfaction. Kerone Engineering is prepared to assist you, no matter where you are in India and overseas.
We Supply and Export in Listed City & States.
Raipur | Bilaspur | Panaji | Vasco da Gama | Gandhinagar | Ahmedabad | Surat | Chandigarh | Faridabad | Gurgaon | Shimla | Manali | Ranchi | Jamshedpur | Bengaluru | Mysore | Thiruvananthapuram | Kochi | Bhopal | Indore | Gwalior | Jabalpur | Mumbai | Thane | Navi Mumbai | Pune | Palghar | Imphal | Shillong | Aizawl | Kohima | Bhubaneswar | Cuttack | Chandigarh | Amritsar | Jaipur | Udaipur | Pali | Jodhpur | Ajmer | Bikaner | Kota | Gangtok | Chennai | Coimbatore | Hyderabad | Warangal | Agartala | Lucknow | Kanpur | Dehradun | Haridwar | Kolkata | Howrah | Itanagar | Naharlagun Dispur | Guwahati Patna | Gaya
Arunachal Pradesh | Assam | Bihar | Chhattisgarh | Delhi |Goa | Gujarat | Haryana | Himachal Pradesh | Jharkhand | Karnataka | Kerala | Madhya Pradesh | Maharashtra | Meghalaya | Mizoram | Nagaland | Odisha | Manipur | Punjab | Rajasthan | Sikkim | Tamil Nadu | Telangana | Tripura | Uttar Pradesh | Uttarakhand | West Bengal
We Supply and Export in Listed Country.
India | Bhutan | Burma | Qatar | UAE | Israel | Italy | Japan | Kazakhstan | Kuwait | Latin America | Nepal | Nigeria | Oman | Philippines | Russia | Sri lanka | Singapore | Sudan | Uganda | US | UK | Europe | Madagascar | Venezuela | Yemen | Ghana | Angola | Malaysia | Peru | Uzbekistan | Saudi Arabia | Morocco | Poland | Canada | Ukraine | Algeria | Argentina | Spain | Colombia | Kenya | Myanmar | South Africa | Tanzania | France | Australia | Thailand | Germany | Turkey | Vietnam | Egypt | Ethiopia | Bangladesh | Brazil | Indonesia | China |